Before I got into accounting, I regularly made fun of my wife’s budgeting habits. Every month, she’d write down all her expenses from the month before in a little diary and calculate how much she’d spent on various credit cards and for utilities. Depending on how the month went, she’d allocate money for the next month.
I look back on those days now and laugh. As an accountant, my life is now dominated by budgets, including the master budget, capital budget, and, the subject of this article, the production budget.
Overview: What is a production budget?
The production budget, or manufacturing budget, is used by accountants and managers to determine how many units need to be produced in a certain period to keep up with demand and manage inventory. There are four components to the production budget:
The production budget formula is:
Ending Inventory + Demand – Beginning Inventory = Production Required
How to create your production budget
Clothes Call makes reflective orange vests that traffic workers wear to be seen by drivers. Usually it takes a few months for permits for traffic work to be completed, which is good for Clothes Call because the company has plenty of lead time on its orders and can accurately forecast demand.
Let’s take a look at its production budget for next month.
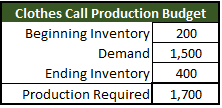
Clothes Call has 200 units left over from last month, and the owner knows the company needs to end this month with 400 units since winter is their busy season. Demand based on current contracts is for 1,500 units to be sold during the month. Using the units of production formula above, we can calculate that Clothes Call needs to make 1,700 new vests this month to keep up with demand and look forward to next month.
Production budget example
I worked at KFC for four years in high school and college. As an enterprising 16-year-old, I decided I wanted to be a supervisor. Many of the supervisor responsibilities were what you’d expect: coordinate where employees would work that shift, complete the closing/opening checklists, make sure food safety guidelines were being followed, etc.
My favorite responsibility was deciding how much chicken needed to be cooked. Fried chicken production may not be where you thought I’d go for my real-world example, but it works perfectly.
When I worked at KFC, it took about 16 minutes to cook a batch of chicken, and we would decide every hour or so how much to cook. Using this example, let’s go over each step of the production budget formula.
Beginning inventory:
Demand:
Production:
Ending inventory:
The fried chicken finished goods formula is pretty straightforward and was designed to make it so 16-year-olds could make decisions on how much chicken to cook. But there was a problem: The chicken predictions were often inaccurate and difficult to apply.
In reality, supervisors typically ordered more chicken to be cooked when they felt like we needed it. KFC probably paid a ton of money to produce the algorithm to predict demand, but, after three or four shifts being caught chickenless at a busy time or throwing out old chicken because it wasn’t purchased, no one paid attention to demand predictions.
And no one had the time to go back to the office every 15 minutes to manually type in how many pieces were cooked, how many were thrown away as waste, and how many were eaten by employees.
There was another inventory control problem as well. Most people bought either a leg and thigh combo (the correct choice) or a breast combo. No one wanted wings. So, at the end of the shift, we would often have 50 or more wings left over. The fancy computer system had no way to enter in that we had 30 wings in the heater but no breasts.
Over time, I got a feel for how much demand would change over different nights, and I would make calls based on that. I would also see what the chicken cooks who had worked at KFC for years thought.
This example is a reminder that production budgets only work if they take into account real-world problems and your business’ unique situation.
Production budget frequently asked questions
Would a production budget only be used for inventory?
To keep it simple, the example above just looked at units required. You could build out the budget even more to include estimates for labor costs and materials to calculate unit production cost.
Where do you keep a production budget?
It’s possible that your accounting software has an option to run production budgets. Otherwise, it’s easy to make one in a spreadsheet if you aren’t dealing with a ton of different products. If you have a more complicated business, you may want to seek out better software.
How important is budgeting in general?
Budgeting is one of the key bookkeeping responsibilities. From 10-house homeowners’ associations to billion-dollar corporations, you won’t find many businesses that won’t benefit from budgeting.
You can go as simple as forecasting an income statement for the year and tracking your progress, or you can make several intense spreadsheets to break down every aspect of your business.
Production junction
Production budgets can be a very effective way to reduce waste and plan ahead in your business. Keep in mind that production budgets can quickly become a classic garbage-in, garbage-out formula if you’re not careful. No matter how much you spend building out the budget, if it has bad inputs or ones that are hard to enter, your employees may decide to totally ignore it.
The post How to Use a Production Budget in Your Business appeared first on The blueprint and is written by Mike Price
Original source: The blueprint