On the invisible tool belt that all business owners wear, there’s one section for financial analysis. If you dig in there, you’ll find metrics like contribution margin to help you price your manufactured goods. Today, we add one more gadget: prime costs.
Overview: What is a prime cost?
Prime costs comprise a company’s direct material and direct labor costs. Businesses calculate prime costs when analyzing manufacturing expenses, efficiency, and profitability.
Direct Labor + Direct Material = Prime Costs
Accountants break down product costs into three categories: direct material, direct labor, and manufacturing overhead. Prime costs are the sum of the first two, which are the direct costs.
Manufacturing overhead houses indirect costs, meaning they aren’t easily traceable to a final product. Businesses allocate overhead costs among their products based on the amount of indirect resources used to manufacture them. Factory rent, advertising, and supervisors’ wages are some of the most common overhead costs.
It’s challenging to allocate overhead accurately, so it can potentially cloud your understanding of a product’s profitability. Comparing prime costs instead can be more telling because it takes imprecise allocations out of the conversation.
Prime costs also mark an item’s rock-bottom selling price; if you sell a product below its prime cost, you’re losing money on each unit. To generate a positive gross profit margin, products should sell for more than their total manufacturing cost, including overhead.
The construction, manufacturing, and restaurant industries most often use prime costs to measure financial performance, but any business that sells inventory can calculate prime costs. At-home Etsy businesses, I’m looking at you.
Prime costs vs. conversion costs: What’s the difference?
Conversion costs are the expenses to turn, or convert, your raw materials into finished goods. It’s the sum of direct labor and manufacturing overhead.
Direct Labor + Manufacturing Overhead = Conversion Costs
Prime costs ignore manufacturing overhead, while conversion costs leave out direct materials. Businesses use both cost formulas to assess profitability and labor efficiency.
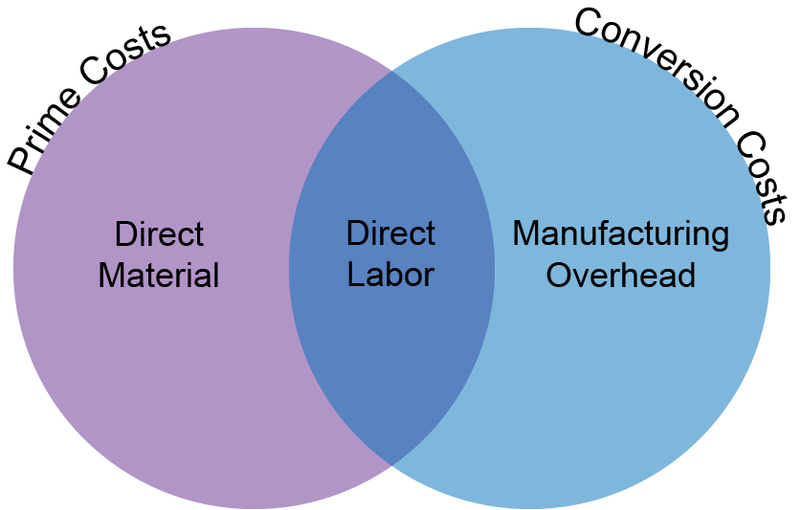
How to calculate prime costs
Before you calculate prime costs, determine all three product costs: direct material (DM), direct labor, and manufacturing overhead.
1. Calculate direct materials
The first element of the prime cost calculation is direct materials, which encompass the physical parts that make up your product.
A woodworker manufacturing a chair would count lumber and fabric as direct materials. Other materials used in production that don’t end up in the final product — such as the gloves, goggles, and masks for the woodworker — are considered indirect materials and are part of manufacturing overhead.
To calculate direct material used in production, use this formula:
Beginning DM Inventory + DM Purchases – Ending DM Inventory = Direct Material Used
2. Calculate direct labor
The next element to calculate is direct labor, or the compensation of factory workers.
There’s no labor cost formula per se, but follow this rule: Direct labor excludes pay for people who aren’t directly involved in work on the making or selling the product. Don’t count Supervisors, janitors, or other workers who weren’t putting your product together.
For example, a woodworker’s wages are considered direct labor, but a supervisor’s pay is indirect labor and would be part of manufacturing overhead.
Direct labor includes the following forms of compensation:
• Hourly wages
• Salaried wages
• Sales commissions
• Benefits
• Bonuses
• Employer payroll taxes
Time-tracking software can help you determine how much time employees spent manufacturing specific products. Sum the manufacturing workers’ earnings to determine direct labor.
3. Sum direct materials and direct labor
The prime costs formula sums direct labor and direct material.
Direct Labor + Direct Material = Prime Costs
Example of prime costs
James owns Snack Shack, a small beachfront restaurant in Miami. He’s looking for an investor who can provide some capital to turn the outdoor patio into the ideal lunch spot before next spring break.
A seasoned business owner, James knows investors will ask about prime costs, a metric restaurateurs often use as a proxy for financial health when compared to sales. Let’s calculate his business’s prime costs for the last calendar year.
1. Calculate direct materials
Start by adding up direct materials. For a restaurant, that’s ingredients, beverages, and other products that end up in front of the customer.
Reusable tableware isn’t considered direct material; as a general rule, direct material must be something the customer can (legally) leave with. However, the little paper umbrellas that adorn every cocktail are counted as direct material since they’re disposable garnishments.
The company’s accounting software shows the following inventory data.
Beginning Inventory | $15,000 |
Purchased Inventory | $395,000 |
Ending Inventory | $10,000 |
Snack Shack used $400,000 in direct materials last year ($15,000 beginning inventory + $395,000 purchased inventory – $10,000 ending inventory).
2. Calculate direct labor
Servers, cooks, hosts, and bussers are the direct laborers at a restaurant. Add up their wages, bonuses, overtime pay, employer payroll taxes, and healthcare benefits.
The restaurant’s worker earnings data is below.
Name | Job | Restaurant compensation | Tips |
Rhonda | Waiter | $15,000 | $22,000 |
Jose | Waiter | $15,000 | $22,000 |
Amelia | Cook | $40,000 | $0 |
James | Owner | $50,000 | $0 |
Snack Shack’s direct labor cost is $70,000 ($15,000 Rhonda’s wages + $15,000 Jose’s wages + $40,000 Amelia’s wages). Since James doesn’t cook or serve, his earnings don’t count in the direct labor calculation.
Don’t include tips in the direct labor calculation since your employees earned them at no cost to the business.
3. Sum direct materials and direct labor
Snack Shack’s prime costs are $470,000 ($400,000 direct materials + $70,000 direct labor).
Now that James knows his prime costs, he can move on to calculating the restaurant’s profit margin, gross margin, and prime costs to sales ratio.
You’ve been primed
Prime cost accounting can help you decide on a product’s selling price or whether to drop a product line in favor of a lower-cost alternative. However, looking at your prime costs is just one way to analyze your business’s financial performance. Check out a host of other financial accounting ratios you can use to take your financial analysis to the next level.
The post How to Calculate Prime Costs appeared first on The blueprint and is written by Ryan Lasker
Original source: The blueprint